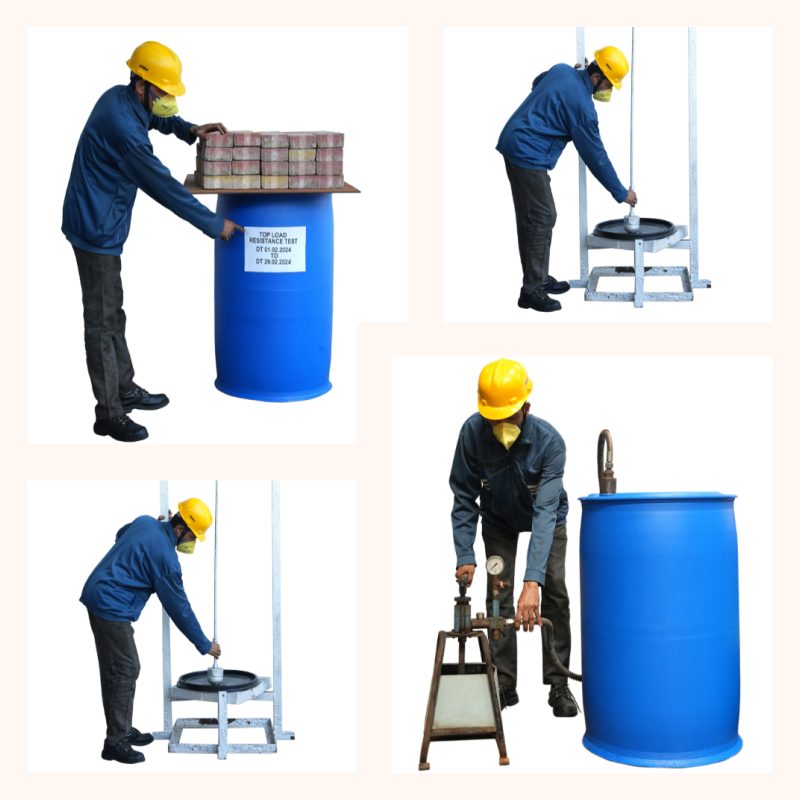
Quality
Quality is our key to success
Machinograph is committed to meet customer’s requirement by providing quality Polycontainers and timely delivery. We are striving for continual improvement through effective implementation of Quality Management System.
Machinograph Is committed to meeting customer requirement by providing packaging which adhere to International standards like UN Code.
Our products also adhere to Indian standards like IS6312. The necessary equipment for maintaining & testing drum quality is available at the labs of our various plants.
TYPES OF TESTS
01
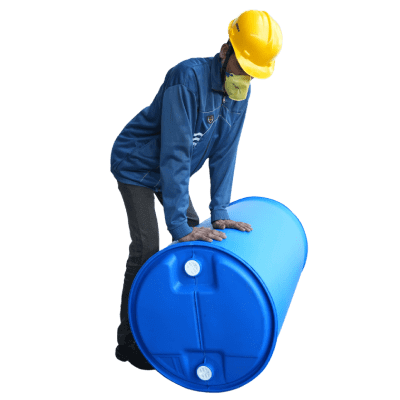
Leakage Test
The Drums are filled with water up to its nominal capacity not up to the brimful capacity of water and the caps are tightened.
TheDrums is then kept inverted on a clean concrete and dry floor. If up to 24 Hours, there is no water leakage in the mouth of drumthen the drum leakage test is passed.
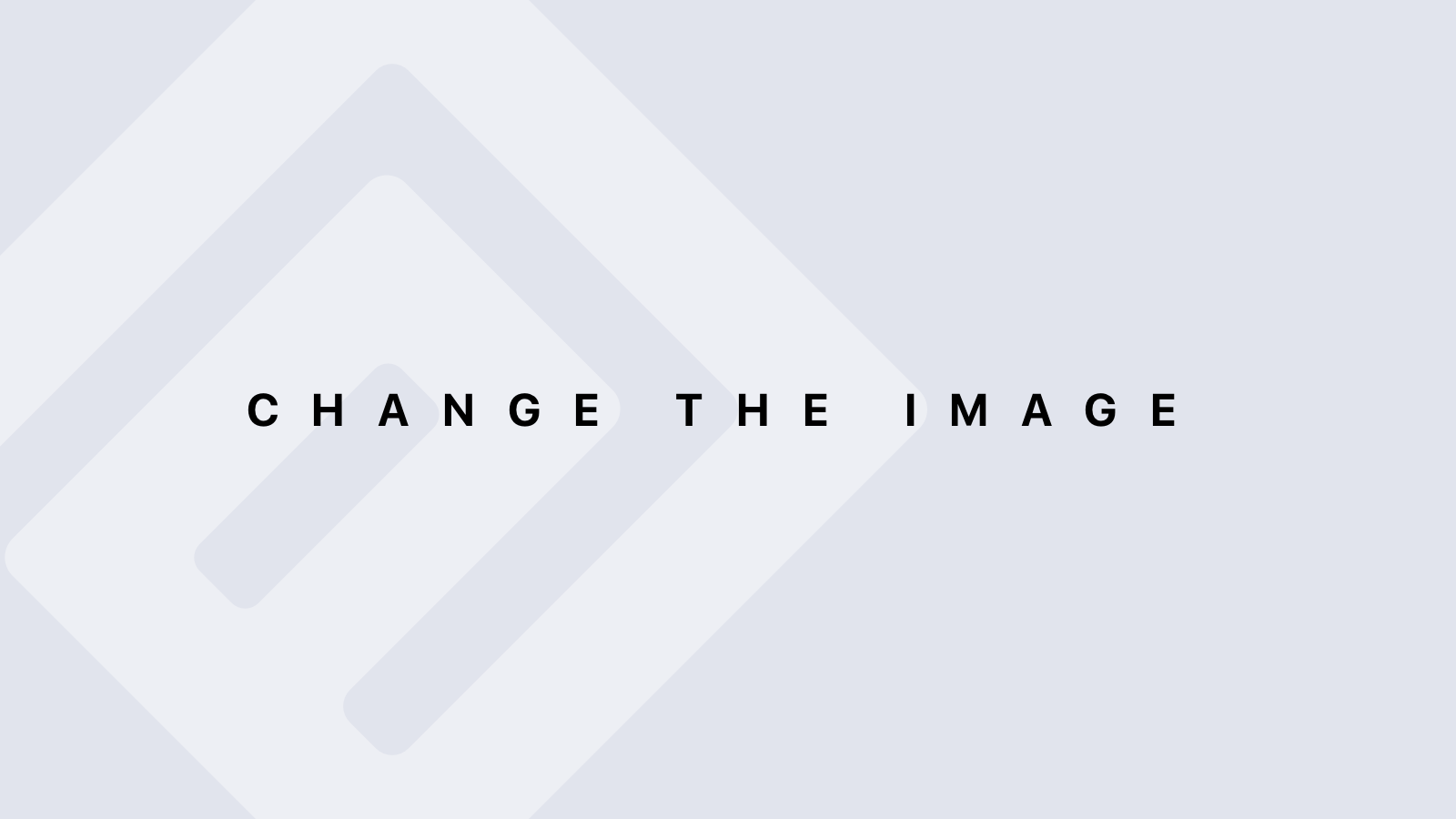
02
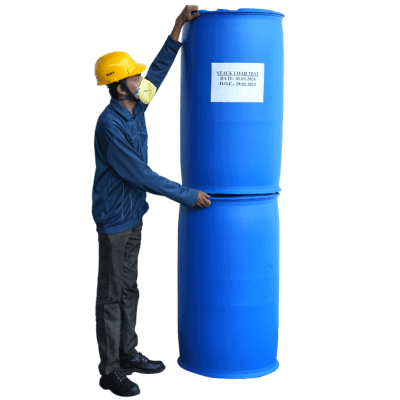
Stacking Test
Two Drums are filled with water up to its nominal capacity not up to the brimful capacity of water and the caps are tightened.
One water filled drum is kept on another water filled drumfor up to 28 days. Periodic observations are made and if no bulging is seen in the body of drums, then the Drum stacking test is passed.
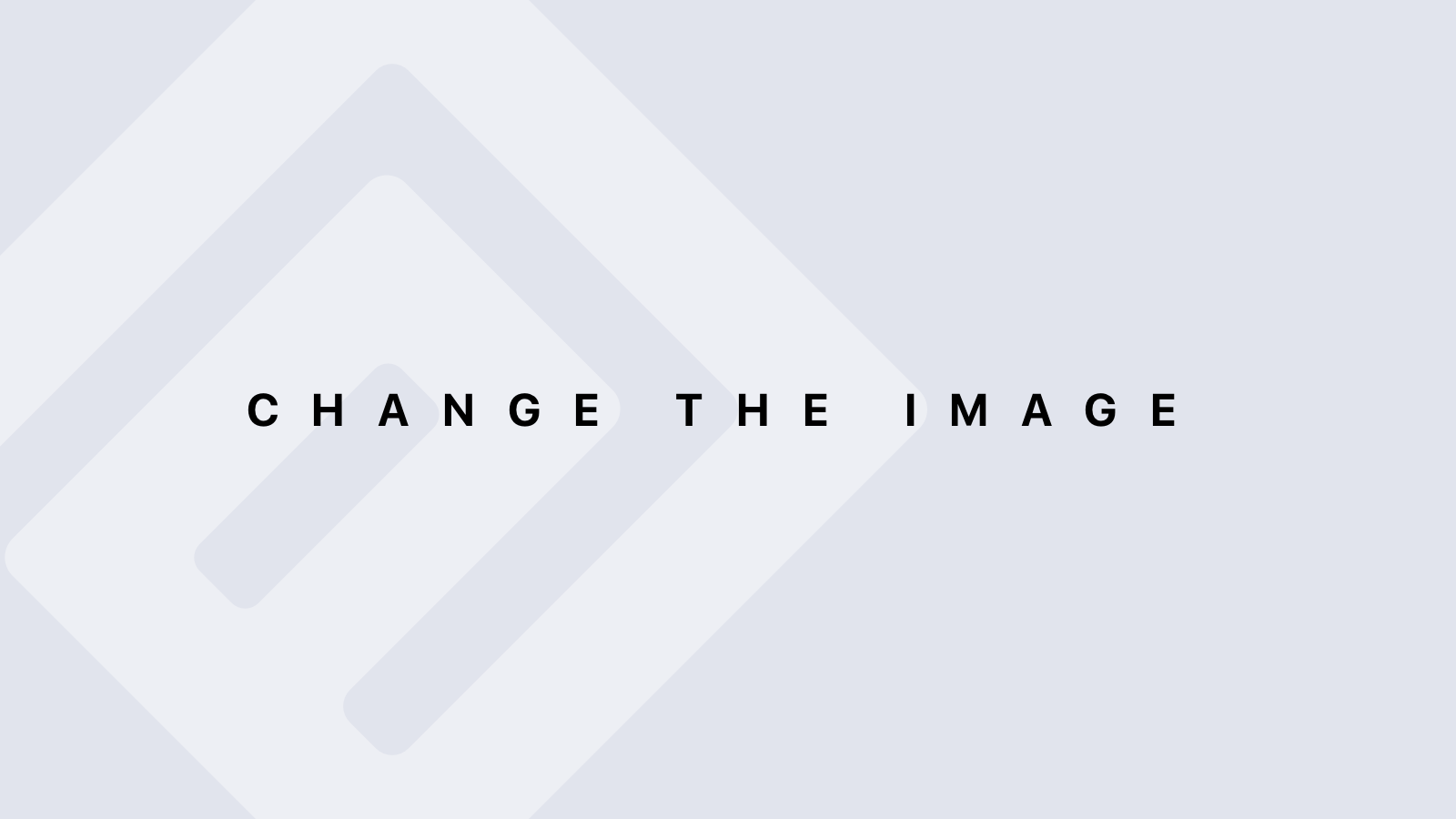
03
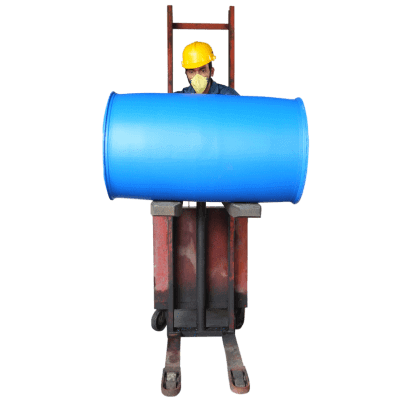
Drop TEST
Drums are filled with water up to (95%) its nominal capacity not up to the brimful capacity of water and the caps are tightened.
The filled drum is lifted up to 1.2 meters by a lifting machine. Each drum is dropped from 1.2 meters, once horizontally and once verticallyat any required angle. There should be no leakages, no ruptures; from the drum then the drum drop test is passed. (Note: Each drum will be dropped only once).
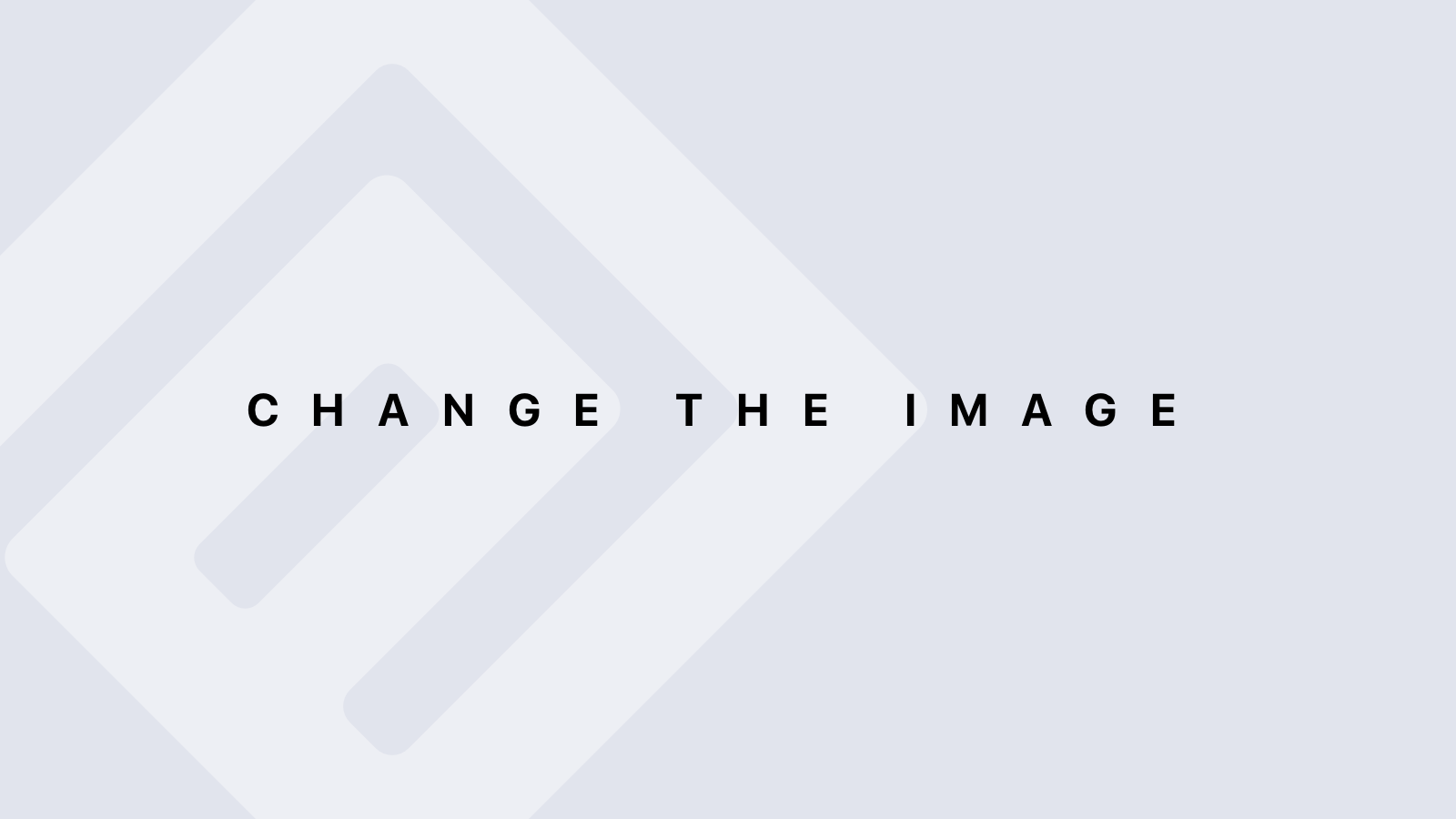
04
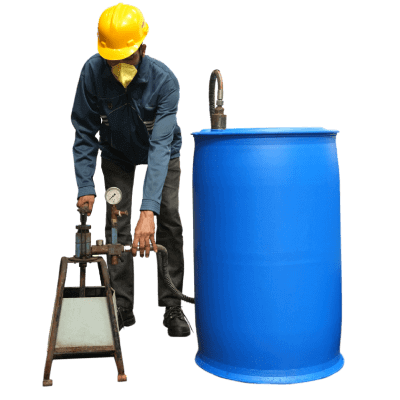
Hydraulic Pressure Test
The drum is filled with water with a gap of 5 ltrs. The cap is tightened only on one side, and the M.S nipple is fitted on other side.
Thereafter the hydraulic machine pipe is joined with the M.S nipple. The hydraulic pump is pressed up to 5.2 psi and then observed for leakages. If no leakages are found then the hydraulic pressure test is passed.
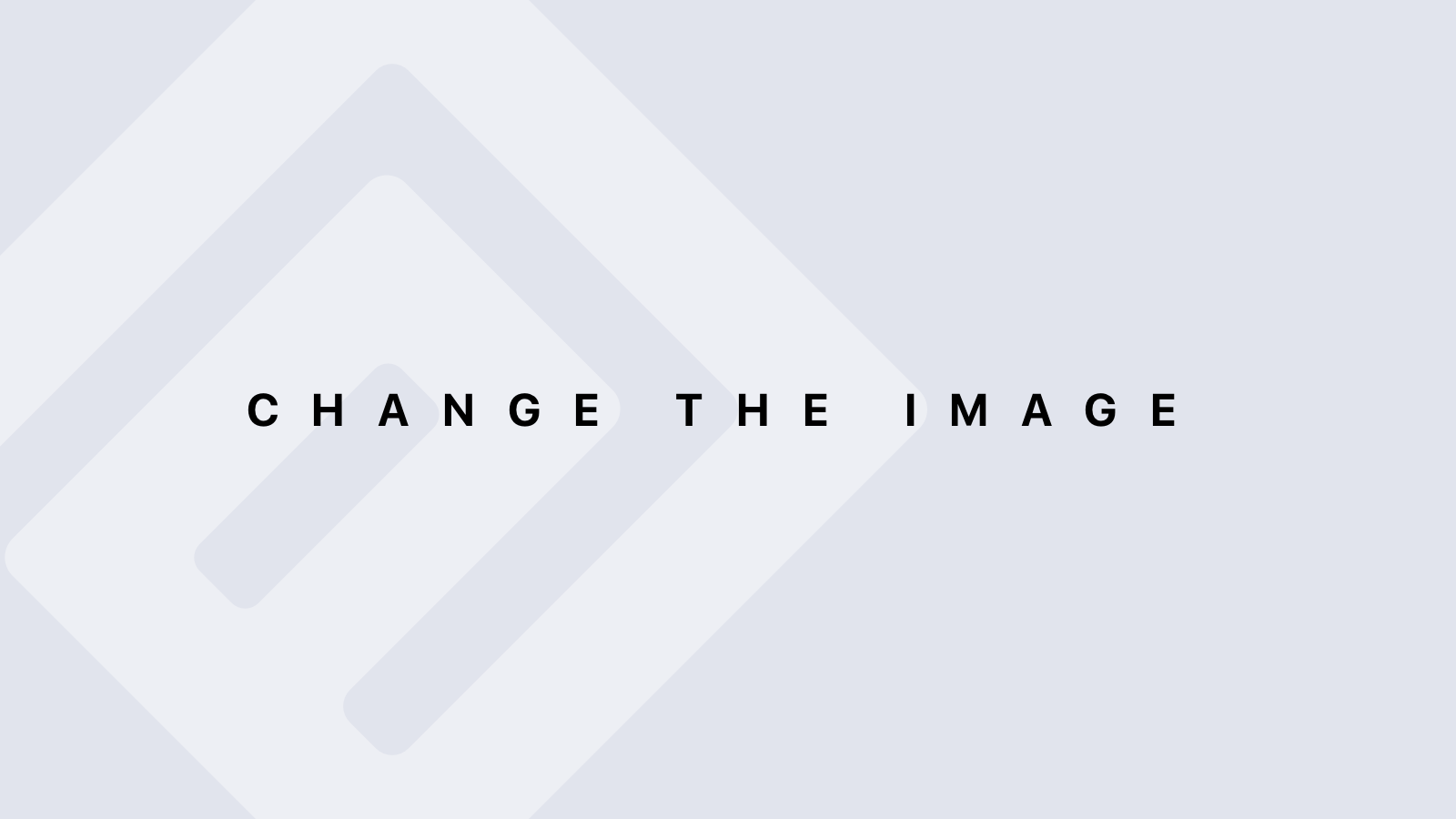
05
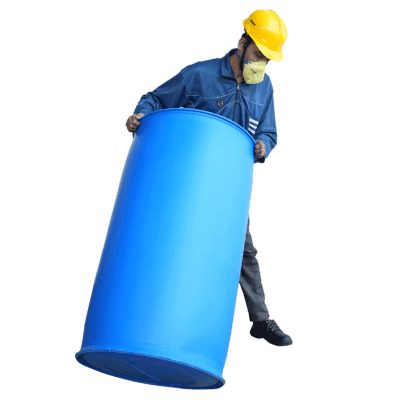
Tilting & Rolling Test
The drums are filled with water up to its nominal Capacity not up to the brimful capacity of water and the caps are tightened.
TheDrum is then rolled up to 10 feet in a 45º inclination and in this position the pressure will come on Bottom of drum. If no bulging is seen on drum then the drum Tilting & rolling Test is passed.
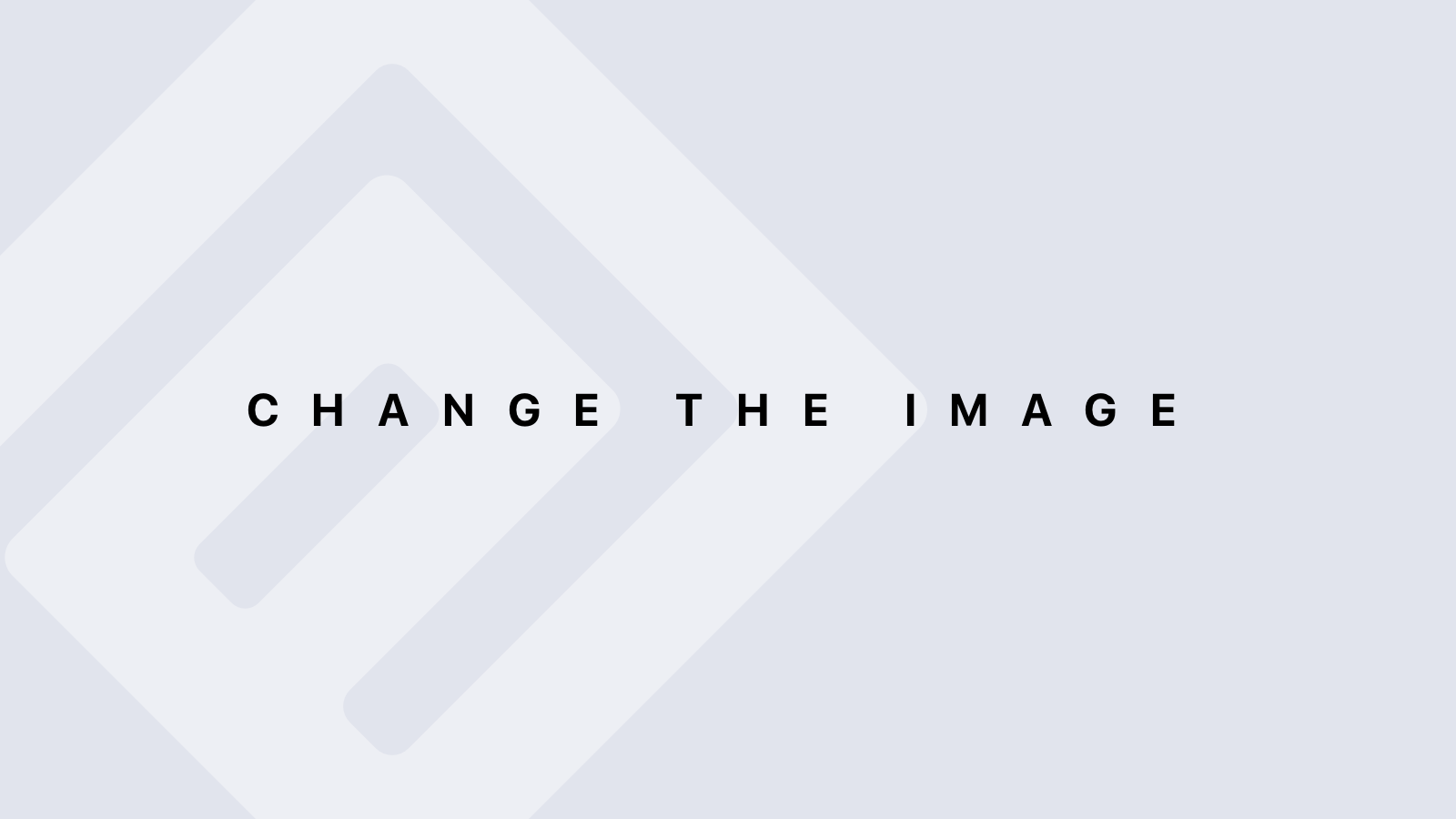
06
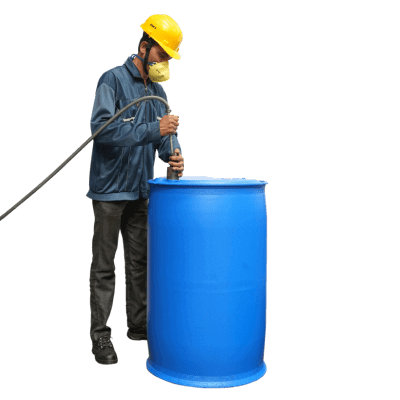
Air Pressure Test
Compressed air is passed through a flexible pipe and a M.S.cap filled with inlet valves as per the following figure.
The Pressure in to the drum is exerted up to 5.2 psi. The compressed air is stopped when pressure reaches upto 5.2 psi (0.75kg/cm3). This drum is then kept in a water bath to check for leakages. If no bubbles are seen coming from the drum’s body,then the drum Air Pressure test is passed
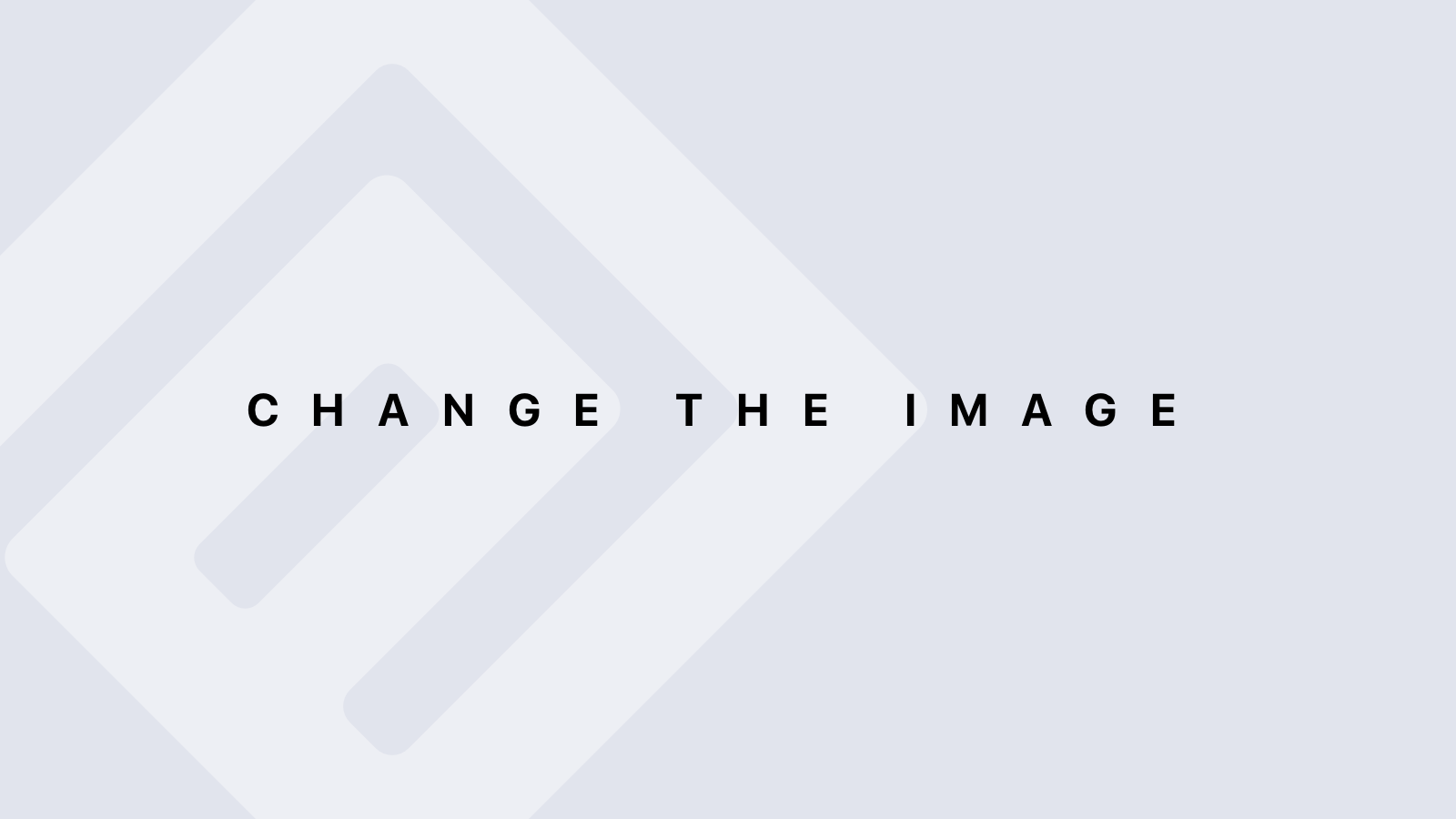
07
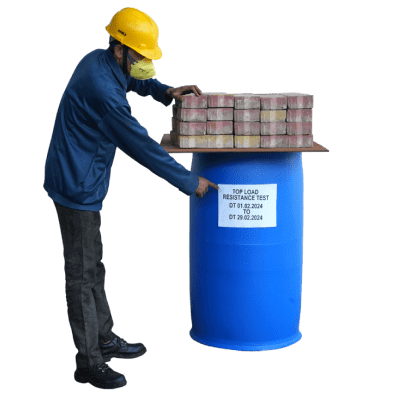
Top Load Resistance TEST
The Drums are filled with water up to its nominal Capacity not up to the brimful capacity of water and the caps are tightened.
Thedrum is then kept vertical on a concrete flat floor. One M.S. sheet of size (3’x 3’ x 6mm) is kept on top of thedrumand 244kg of bricks are kept on the metal sheet maintaining a uniform load distribution. Date of initiation oftesting is stuck on the drum belly. The drum is observed periodically up to 28days. If no bulging is observed during the period of 28 days, then the top load resistance test is passed.
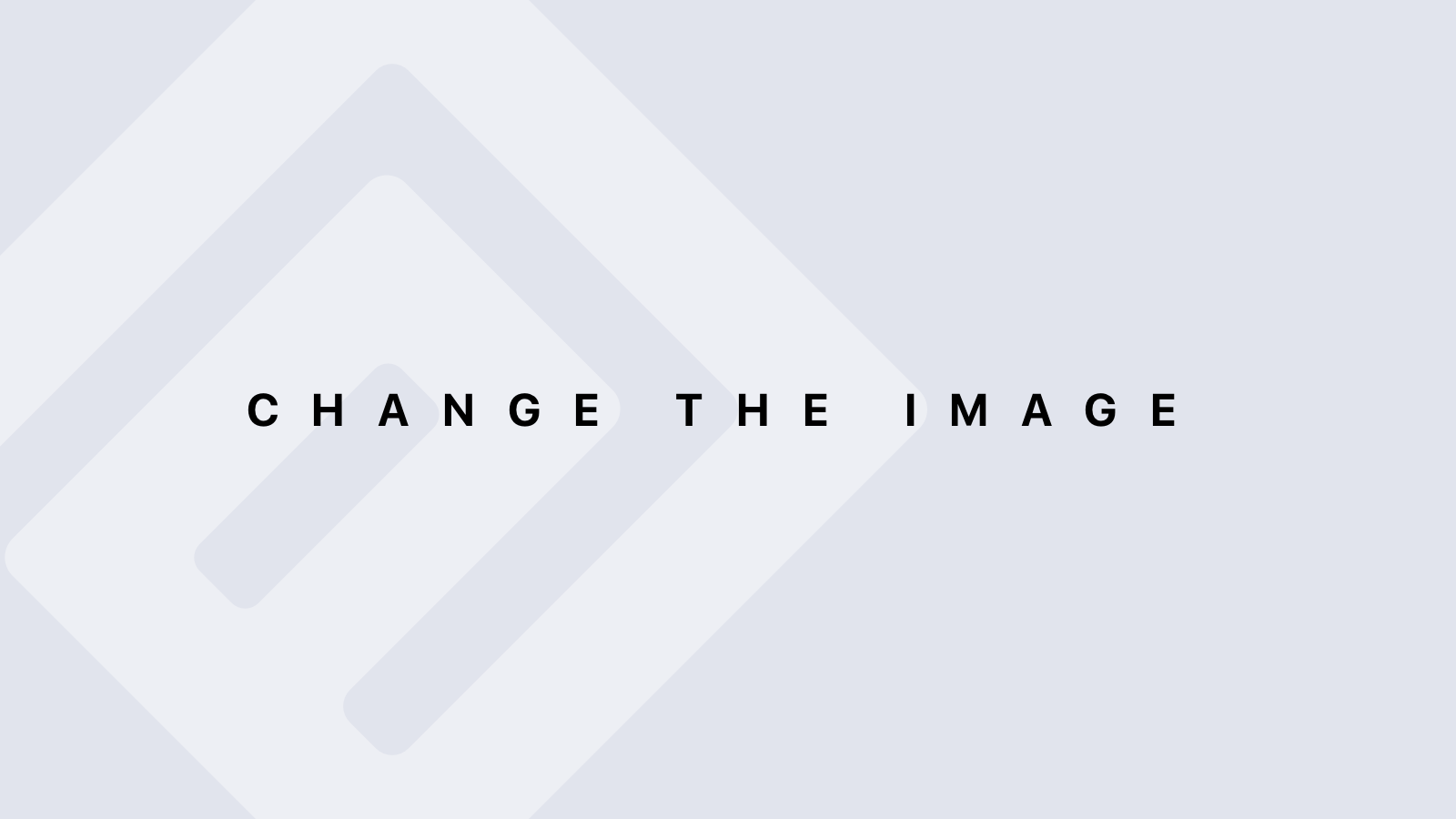
08
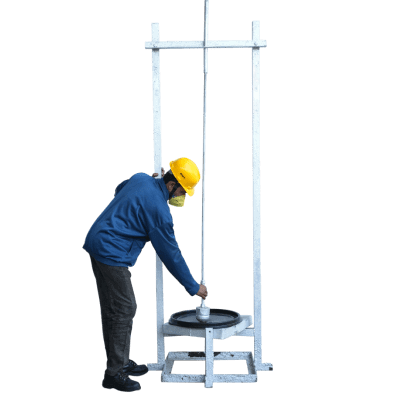
Drum Cap Testing
Cap testing equipment is used to check the strength of caps produced. The sample cap is kept on the bottom base of equipment
and a weight of 8 kg is dropped from a height of 5 feet. This procedure is repeated 3 times. If there is no rupture or crack found on cap, then the testing is passed.
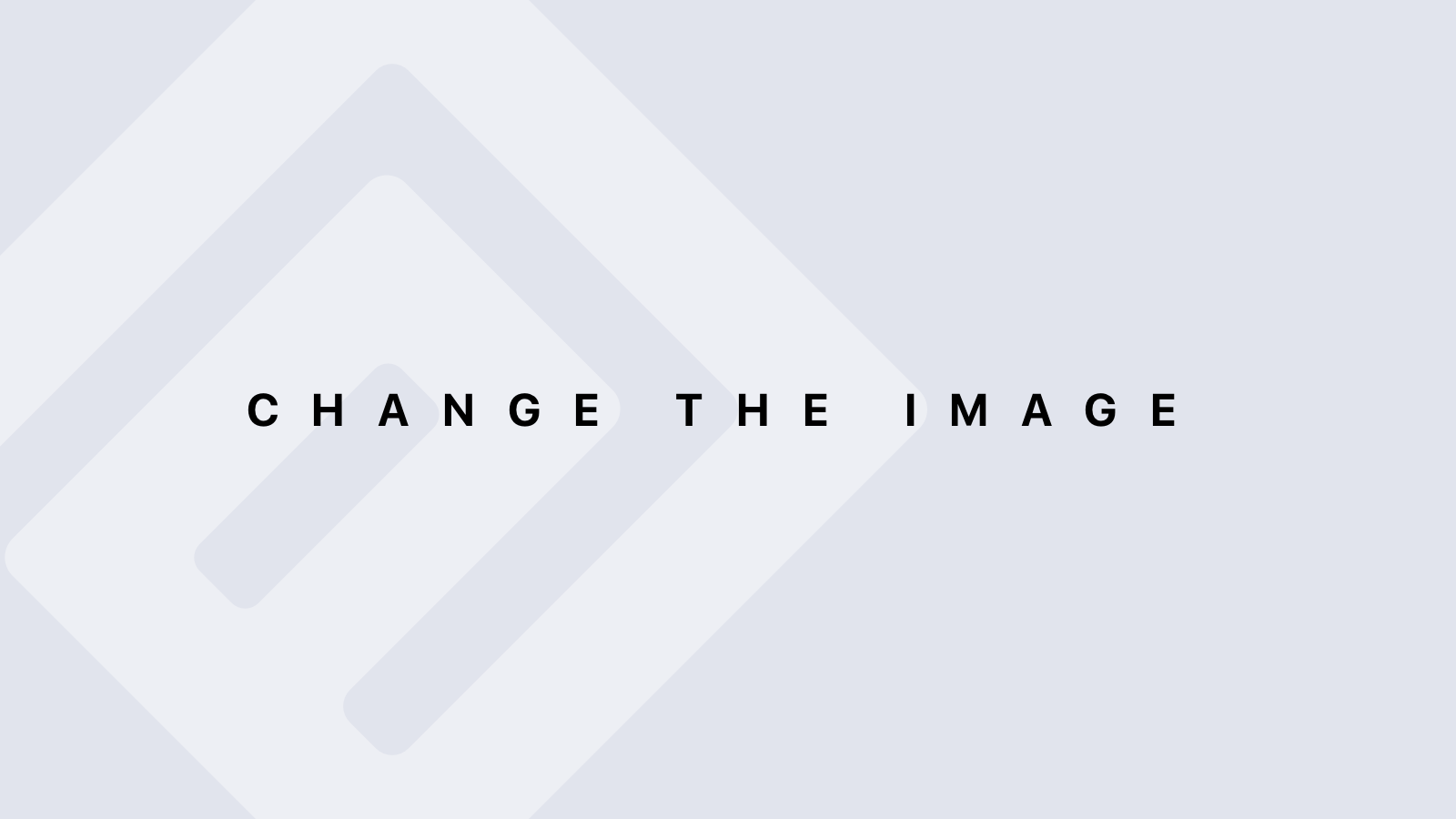
09
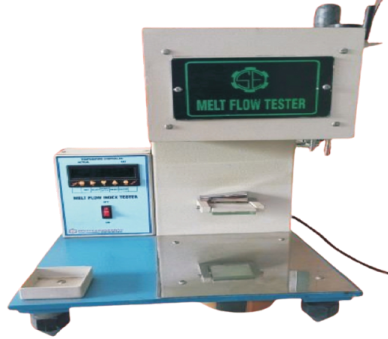
MFI Testing
MFI is a simple measurement of the quality of polymer pushed through a die of specified dimensions at a set temperature within 10 min.
It is frequently used to compare grades of the same polymer, as it gives an indication of the melt flow index present in that batch or grade.
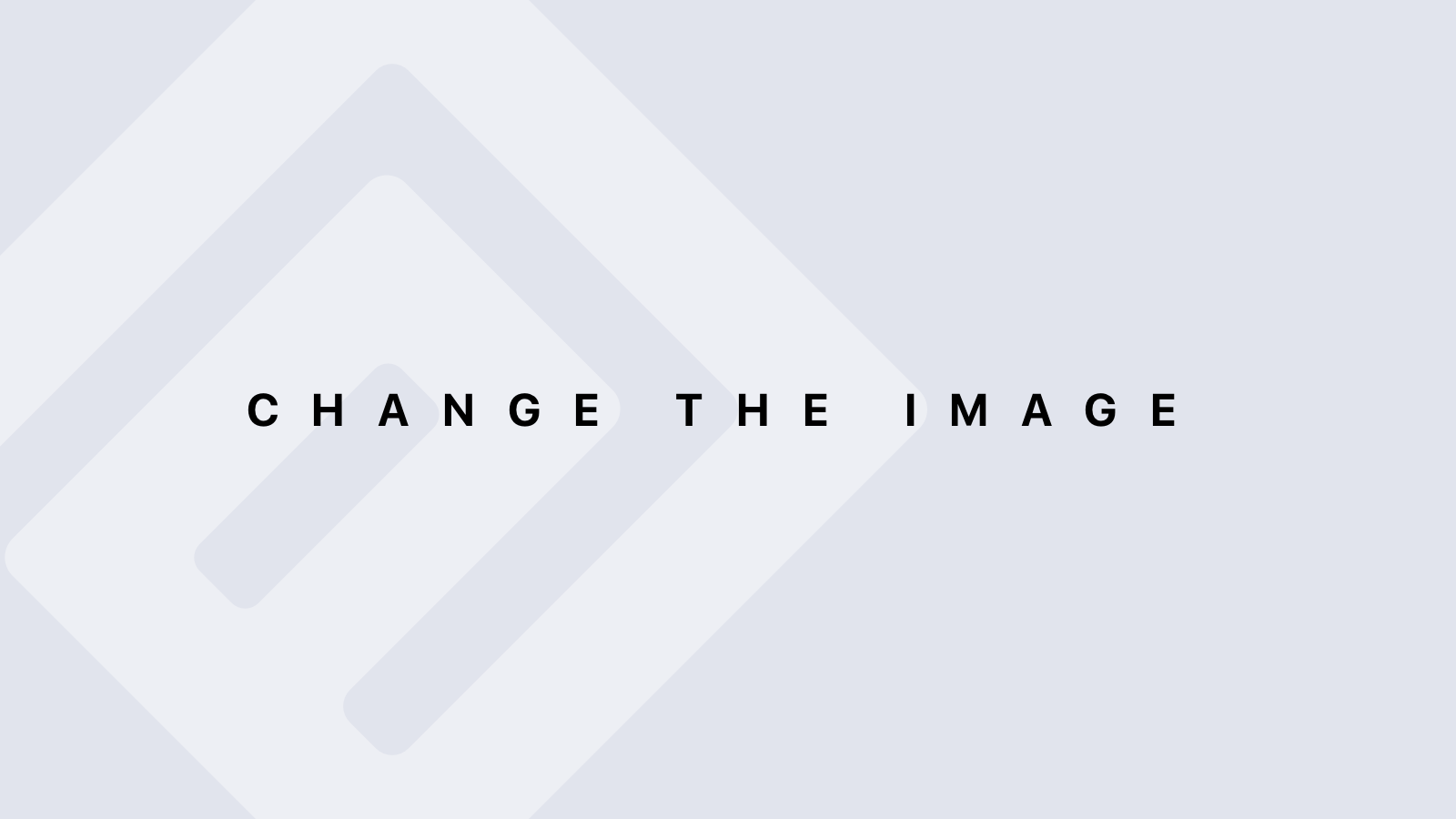